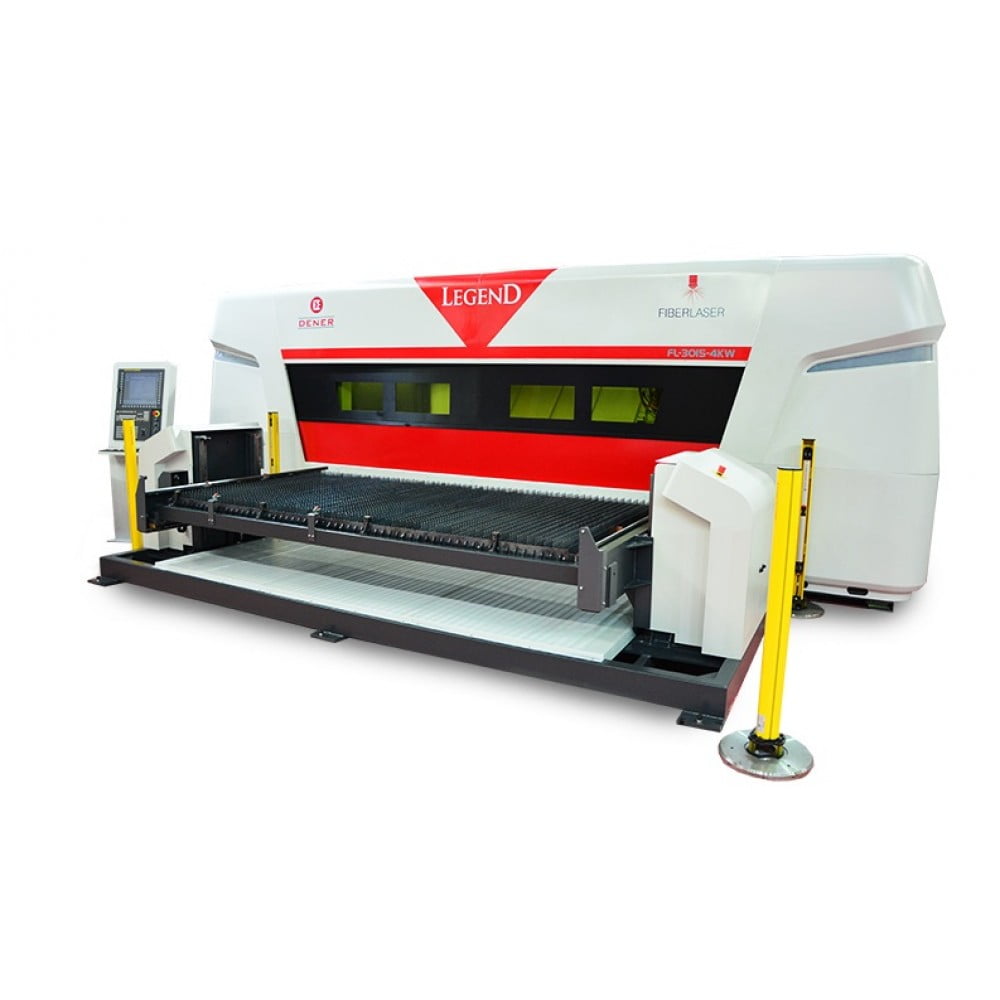
Sac İşleme, Bükme, Kesme Makineleri ile ilgili bu yazıda makinalar hakkında açıklayıcı bilgiler, kullanım şekilleri, marka bilgileri, fiyatları bulunmaktadır.
Günlük hayatımızda kullanmış olduğumuz tüm metal ekipmanlar çeşitli işlemelerden geçerek oluşturulmaktadır. Metal işleme teknolojisini ana hatları ile iki gruba ayırabiliriz. Talaşlı imalat makinaları ve Sac işleme makinaları olarak. Talaşlı imalat grubu ile ilgili olarak Nicemak’ ın ilgili kategorisinden incelemelerde bulunabilirsiniz.
Sektör makine üreticileri incelendiğinde kullanılan komponetleri farklılığına göre makineler fiyatlandırılmaktadır. Fiyat olarak incelendiğinde rakipler ile teknik özelliklerin incelenmesi gerekir. Segmenti belli olan ürün gruplarında fiyatlar incelendiğinde maksimum +/- %5 oynamaktadır. Fiyatlar arasından %20 gibi bir fark bulunuyorsa aynı segment değildir.
Hangi ürünü alırsanız alın ilk etap hepsi iyi görünmektedir. Kullanılan ekipmanlara göre kalitesi zamanla belli olmaktadır. Makine yatırımları olmadı satıp değiştirelim diyebileceğiniz ucuz yatırımlar değildir. Bundan dolayı alım aşamasında iyi incelemek gerekmektedir.
Bu bölümde sac işleme makinaları hakkında ürünler sunulmaktadır. Makinalar hakkındaki bilgiler her kategori içerisinde yar almaktadır.
Abkant Pres Nedir, Nerelerde Kullanılır?
Sac işleme makinaları içerisinde şekillendirme açısından Apkant pres önemli bir yer tutmaktadır. Piyasada eski tabiri ile caka, bükme, pres, abkant pres gibi isimler ile anılmaktadır.
Bilindiği gibi sacı şekillendirmek için belirli bir baskı ile alt ve üst kalıplar arasında sıkıştırarak şekil verilmektedir.
Geçmiş dönemlerde Eksantrik apkantlar kullanılıyordu. Teknolojinin gelişmesi ile apkantlar Hidrolik Apkant pres olarak adlandırıldı. NC kontrol sistemi kullanılması ile öğretmeli bir şekilde program yazılmaya başlandı. Bu tip apkant preslerin tek pompadan tahrik ediliyor olması ile büküm sırasında dengesizlikler meydana geliyor ve Stoper mili dedikleri mili kırıyordu. CNC kontrol sistemi ile tüm bükümler için program yazılabilir hale geldi. Hibrit Apkant Pres olarak isimlendirilen Apkantlar üretilmeye başlandı. Burada CNC kontrol ile pistonlar üzerindeki pompalara gerekli gücü sağlayan servo motorlar kullanıldı. Enerji tasarrufu anlamında günümüzde kullanılama devam edilmektedir.
Teknoloji ile birlikte hidrolik piston sistemi olmadan büküm yapabilecek Servo Apkant pres olarak isimlendirilen kayış kasnaklar ile güç sağlanan apkant presler üretildi. Detaylarını girildiğinde birçok avantajı beraberinde getirmiş oldu.
Havalandırma sisteminde kullanılan Caka olarak adlandırılan, aşağıdan yukarıya doğru kaldırılarak büküm yapılan makinalara Caka ismi veriliyor. Bu günümüzde CNC kontrollü ve manuel olarak da aktif olarak kullanılmaktadır.
Hidrolik CNC Apkant Pres
Hidrolik güç ile 40 ton’dan 2000 Ton’a kadar, 1.5m boydan toplamda 16 metre boya kadar Hidrolik apkant presler üretilmektedir.
Hidrolik Apkant pres teknolojisi incelendiğinde genel Apkant üreticilerinde bulunan üç model karşımızda çıkmaktadır.
Ekonomik Apkant pres, genel olarak firmaların sür bük olarak tarif edilen ekstra fonksiyonel özelliklere ihtiyaç duymadığı CNC kontrol ile program yapılan hidrolik apkant yapılmaktadır. Bu serilerde arka dayamanın aşağı yukarı hareketi (R ekseni) manuel olarak ayarlanmaktadır. Basit 2D bir görsel sunan 4 eksen hareketini kontrol eden bir kontrol sistemi kullanılmaktadır. İlave olarak R ekseni eklenmektedir. Makine üreticisine göre değişkenlik gösterse de manuel AC bir motor kullanılarak Ncoder ile mesafe tayini yapılmaktadır. Servo sisteme göre daha yavaştır. Ayrıca kullanılan Ncoder in kalitesi milimetrik hassasiyeti de belirlemektedir.
Üst sınıf Apkant Pres , Bu apkant preslerde genel olarak kullanılan ekranlarda 2D çizim ve 3D görsel sunmaktadır. 2D olarak çizdiğiniz bir görüntünün boyunu girdiğinizde size 3D bir görsel sunmaktadır. Bazı makine üreticilerinde Dener firmasında 3D programlama ve 3D görsel sunmaktadır. Diğer üreticilerde bu ekran için ekstra ücret ödemek gerekmektedir.
Eksen olarak isimlendirilen tüm hareketler bu yapıda bulunan preslere ilave edilebilmektedir. Standart olarak 4 eksen olarak üretilmektedir. Bursa eksenleri inceleyecek olursak, Hidrolik pistonların kontrolü Y1 – Y2 ekseni, Arka dayamanın ileri geri hareketi X ekseni ve arka dayamanın aşağı yukarı hareketi R ekseni olarak isimlendirilir. R ekseninin avantajı büküm sırasında dayamanın aşağıda veya yukarıda olması gerektiği programdan yazıldığı için parçayı tek seferde bükmenizi sağlar. Olmaması durumunda yarıda bırakıp elle ayarlayıp büküp sonra tekrar ayarlamanız gerekmektedir. Piyasada bir işi birkaç kez elimize alıp bükmeyi elleşme olarak adlandırırlar.
Arka dayamaların sağa ve sola hareketleri manuel olarak yapılmaktadır. Bu hareketin CNC kontrol üzerinde yapılması Z1 – Z2 ekseni olarak adlandırılır. Bu özelliğin bulunması sıralı parçalı kalıplı bir bükümünüz varsa büküm sırasında arka dayamanın sizi takip etmesi sağlanmaktadır. Bu tarz bükümlerde elleşme tabirini ortadan kaldırarak tek seferde bükümleri bitirmemizi sağlamaktadır. Piyasada genel olarak bu özellik istendiğinde 6 eksenli olarak alınırlar (Y1-Y2-X-R-Z1-Z2).
Arka dayamanın ekseni bir hat üzerinde bağlı, birbirinden bağımsız hareket edememektedir. Bur durumda arka dayamanın birinde motorlu bir mekanizma ile belirli bir mesafede ileri geri hareketi yapan piyasada X-Prime olarak veya Delta X olarak adlandırılan eksen kullanılmaktadır. Arka dayamada örnek olarak bir bükülecek sacın bir tarafında 100mm diğer tarafında 125mm ölçüsünde dayama yapılması gerekiyorsa bu eksen, istenen bu özelliği sağlamaktadır. Bir başka örnek parmaklarınızı birleştirdiğinizde yandan bir dayamanın işaret parmağınızda bir dayamanın başparmağınızdan dayaması gerektiği gibi düşünülebilir. Bu tarz bir apkant pres 7 eksen olarak adlandırılır.(Y1-Y2-X-R-Z1-Z2-X prm).
X hareketinde ileri geri hareket mesafesi yeterli olmadığından arka daymanın bütün halinde çapraz hareketler yapması X1-X2 Ekseni olarak adlandırılır. 7 eksen olarak isimlendirilir (Y1-Y2-R-Z1-Z2-X1-X2).
Bazı durumlarda arka dayamada R ekseni mesafesinde bir dayamanın aşağıda bir dayamanın yukarıda olması istendiğinde arka dayamanın birbirinden bağımsız hareket etmesi gerekmektedir. Arka dayama bir birbirinden bağımsız sağa sola, ileri geri, aşağı yukarı, hareket edebilir. Bu şekilde arka dayman 6 eksen hareketi ve hidrolik pistonlardaki eksenler ile birlikte 8 eksen olmaktadır (Y1-Y2-R1-R2-Z1-Z2-X1-X2).
Hibrit apkant pres, Hidrolik pompaya basınç bir motor sayesinde alınmaktadır. Siz apkant ekran olarak çalıştırır devamında motoru açarsınız hidrolik pompa basınç vermediği durumlarda motor boşta çalışma ile %20 enerji harcayarak devamlı olarak dönmektedir. Siz pedala basarsınız büküm işlemi için ne kadar güç gerekiyorsa onu kullanır bitiminde tekrar boşta çalışmaya devam eder. Burada muazzam bir gereksiz enerji kullanımı bulunmaktadır. Geliştirilen hibrit teknolojisi ile buradan bulunan pompalara güç veren tek motor yerine piston üstlerinde bulunan Servo motor ile hareket verilmektedir. Bu şekilde siz pedala basmadığınız sürece sadece kontrol ünitesi enerji harcamaktadır. Pedala bastığınız sizin için yeterli olarak güç oranına göre enerji harcayıp tekrar geri kalkacaktır. Örnek olarak 10 mm bükme kapasiteli apkantınızda 3 mm için harcadığınız tonaj ile 10mm arasında fark oluşacaktır. Bunlarda göz önünde bulundurulduğunda hibrit apkant presler %70 oranında enerji tasarrufu sağlamaktadır. Ayrıca Kullanılan yağ tankı kapasitesi düştüğü için çevre dostu bir apkant pres olmaktadır.
Ayrıca Tüm Hidrolik apkant preslerde kullanılan bombeleme sistemi vardır. Eknomik makinalarda bu sistem manuel özellikli apkantlarda motorlu olarak kullanılmaktadır. Siz 3 metrelik bir apkant preste 3 metre bir büküm yapmak istendiğinde pistonlar sağ ve sol başta olduğundan baskı sırasında orta noktalarda basınç olmadığı için kuvvet vektörleri sağa solar giderek azalmaktadır. Kenarlara örnek 100 ton uygularken orta notkata 90 ton yük uygulanmaktadır. Bu durum sizin büküm parçanızda kenarlarda 90 derece orta noktada 100 derece olmasını sağlar. Eski sistemlerde bunu düzeltmek için kalıp altına gazete kağıdı konuluyordu. Sonrasında bu güç dengesini sağlamak amacı ile alt tablanın ortasını yukarı doğru kaldırmak gerektiği için kamalı sistem ile orta nokta yukarı kaldırılarak her yerde aynı açı değerini yakalaması sağlandı. Manuel olan sistemde büküme, malzeme cinsine göre numaratör üzerinden ayarlamanız gerekiyor. Üst sınıf Apkant preslerde bu sistem motorlu olarak girilen malzeme cinsi ve boyuna göre otomatik olarak ayarlanmaktadır. Hassas işler bu dengeyi sağlamak biraz zorlaşmaktadır. Çünkü Y1-Y2 dengesi Bombeleme yüksekliği çeşitli denemelerden sonra size doğru ürünü üretmenizi sağlamaktadır.
Servo Apkant Pres
Hidrolik Apkant preslerde yağ sıcaklığına bağlı yağın viskozitesi değişiklik gösterdiğinde kullanım sırasında zamanla bükümler aynı dereceyi tutturamama problemleri ile karşılaşılmaktadır. Bombeleme sistemine gereksinim olduğundan açısal problemler yaşanmaktadır. Hidrolik sistemde bağ ön dolum ve basınç için zaman ihtiyaç olduğundan genel olarak büküm hızları 10 mm/sn hızları aşmamaktadır. İstenirse bu hız arttırılabilir ancak bu zamanda tekrarlanabilirlik hassasiyeti bozulmaktadır. Bunun gibi farklı nedenlerden dolayı Servo apkant pres teknolojisi kullanılmaya başlandı. Servo apkant preste hidrolik sistem bulunmamaktadır.
Vidalı Milli Servo Apkant Pres,Küçük bükme ölçülü Servo apkantlar Vida milli olarak adlandırılır. Vidalı mil üzerinde bulunan bir servo motor ve rediktör sayesinde güç mil üzerinden aktarılarak büküm işlemi gerçekleştirilmektedir. Bu sistem 600mm ve 900mm apkantlarda kullanılmaktadır.
Servo Apkant Pres, Büküm boyu dener Ar-Ge çalışmaları ile 4 metre 200 tona ve 3 metre 220 tona kadar üretilmektedir. O gövde olarak adlandırılan bir gövde yapısına sahiptir. Sağ ve sol kenarlarda bulunan servo motorlar Tabla orta noktasında bulunan bir noktaya bağlanan kayış makarası sistemi ile gücü arttırıp büküm işlemini gerçekleştirmektedir. Yüzeye uygulanan basınç hep dik olduğundan güç kaybı meydana gelip motorlu bombelemeye ihtiyaç kalmamaktadır.
O tipi olarak adlandırılan gövdenin bir avantajı C tipi olan Hidrolik apkant preslere göre Muz olarak tabir edilen yapının oluşmamasıdır. C tipi gövdede basınç sırasında C gövdede yukarı doğru bir elastik deformasyon hissedersiniz yukarı doğru açıldığını basınç sonrasında tekrar eski hali aldığı görülür. O tipi gövdede bu arz bir esneme meydana gelmemektedir.
Bükme hızı iş güvenliği tedbirleri alındığında 20 mm/sn hızlarda kullanılmaktadır. Yağ sistemi olmadığından tekrarlamada herhangi bir problem ile karşılaşmazsınız. Robotik büküm istasyonlarından Servo apkant ile 24 saat çalışabilirsiniz.
Caka Makinaları
Genel olarak ince sac parçalarda kullanılan caka Mekinleri, Apkant presteki gibi çok farklı alt ve üst kalıp olması zorunluluğu yoktur. Alt tabladan yukarı yönlü hareket ile istenen mm ölçülerinde bükümler yapılabilmektedir. Havalandırma sektöründe kullanımı oldukça yaygındır. Bazı modellerde üst tablada parçalı kalıp kullanılarak tava bükümlerinde kullanılabilir. Apkant pres yatırımından çok daha ekonomiktir.
Yurt dışı üretimi olan CIDAN benzeri CNC caka makinaları da bulunmaktadır.
Manuel ve Motorlu Caka Mekineleri
Manuel caka makinalarında Parçalı bıçaklar sayesinde değişik ebatlarda kutu şeklindeki imalat yapılabilir.
Oynak çenenin hareketi, güçlü yaylar ve manuel kolla gerçekleştirilmektedir. Bu tiplerde sacın sıkıştırılması için üst çeneye herhangi bir ayar gerekmez. Bazı modellerde Motorlu caka makinaları da bulunmaktadır. Redüktör yardımı ile tablanın yukarı kalması sağlanarak bükümler yapılabilir.
CNC Caka Makineleri
CNC Caka Makinaları içerisinde çok farklı opsiyonlu makineler bulunmaktadır. Program yazılarak arka dayama mesafesinden sacı istenen ölçüye kadar öne sürer ve büküm işlemi gerçekleştirilir. Sıralı büküm varsa tüm bükümleri programlayarak büküm işlemi gerçekleştirilir. Sonrasında sacı döndürmek gerekiyorsa manuel olarak döndürüp işlemler tekrarlanabilir. Farklı üst modellerinde sacı otomatik olarak döndürüp size bitmiş ürün olarak sunmaktadır. Ters bükümler gerektiğinde üst tablanın aşağı yönlü hareketi olan modelleri de bulunmaktadır. İnce saclı seri kabin işleri yapan firmalarda aktif olarak kullanılmaktadır. Normal apkantta kalıp değişimi ve sizi bağlayıcı olaran dar etek paylı bükümlerde profesyönel çözümler sunmaktadır. Fiyat yatırımı anlamında analiz edildiğinde yüksek gibi görünebilir ancak birim zamanda üretim adedi ile amortisman süresini kısaltmaktadır.
Giyotin Makas
Sac şekillendirme makinalarında zaman içinde farklı teknolojiler geliştirilse de Giyotin Makas güncelliğini her zaman korumaktadır. İstemiş olduğunuz bir ölçüye sacı getirmek için levhadan çeşitli ölçülerde kesmeniz gerekmektedir. Giyotin Makaslar tarihi incelendiğinde de motor kuvveti ile kesilen eksantrik makas ile başlayan serüven, ağır parçaların da kesilmesini sağlayan Hidrolik Giyotin makas halini almıştır. Arka dayama sistemi elle ayarlanan arka dayamadan, sonrasında dijital ekran ile mesafe girmeye geçildi. Nc kontrol sistemlerinin gelişmesi ile ekran üzerine program yazılarak arka dayama istenen ölçüye getirildi. Adet olarak bilgi girildiğinde istenen adet sağlandıktan sonra kesimi bitirdi.
Hidrolik giyotin makaslarda hidrolik sistem olduğundan dakikadaki vuruş adedi düşüktür. Siyah 4mm kadar İnce parçalarda ise seri bir kesme istenmektedir. Bu durumda da redüktörlü giyotin makaslar kullanılmaktadır.
Giyotin makaslar malzemeyi yarısına kadar kesme yarıdan sonrasında koparma işlemi ile kesmektedir. Malzemede koparma işlemi sırasından bağlar koparken 45 derecelik bir acı ile kopmaktadır. Kesim yüzeyinden incelendiğinde Kesilme ve kopma net olarak görülmektedir.
Giyotin makaslar genel olarak sınıflandırıldığında Kollu giyotin makas, Redüktörlü giyotin makas, NC devirmeli Giyotin makas ve CNC Açı ayarlı giyotin makas olarak sınıflandırılmaktadır.
Hidrolik Giyotin Makas
Giyotin makas ile kesebilmek için alt ve üst kalıp arasındaki boşluğu ayarlamamız gerekmektedir. Bıçak boşluğunu NC Kontrollü Devirmeli giyotin makaslar yan tarafta bulunan kol üzerinden kesilecek mm göre ayarlanmaktadır. Bazı modellerde yandan motorlu bıçak boşluğu ayarlanabilir. Genel olarak devirmeli giyotin makaslarda kesme açısı 2.30’ derece ile malzemeye girmektedir. Çalışma sistemini örneklendirecek olursak elimizi masanın kenarına dayayalım, arada oluşturacağımız boşluk kesmemiz gereken mm kalındığına göre iler geri hareket ettirmemiz gerekir. Minimum 0,5mm kalınlığına kadar kesimler yapılabilir. Çok elzem istenirse bu ayarda ayarlamalar yapılabilir. Sağ kol ile sol el arasında bir açı verdiğimizde kesme açısını ayarlamış oluruz. Dirseklerimizden aşağı yukarı hareket ettirdiğimizde kesme işlemini yapmış oluruz. Tablanın aşağı yukarı hareketini hidrolik sistem ile gerçekleştiririz. Giyotin makas tekrar yukarı kalması için gecen zamanı hızlandırmak için küçük bir azot tüpünden yararlanmaktadır.
CNC makinalarda ise üst tablada dikey 2 piston bulunmaktadır. Tabla hareketini ve kesme açısını buradan ayarlamaktadır. Pistonlardan kesme açışını 0.30’ kadar indirilebilir. Bıçak boşluğu tabla arkasında bulunan mekanizma ile motorlu olarak ayarlanmaktadır. Genel olarak Paslanmaz malzeme kesimi yapan firmalarda kesim açısı önemli olduğundan CNC makine tercih etmeleri daha iyidir.
İnce saclarda malzemeyi sürdüğümüzde arka dayamaya ulaşamadan sac aşağı doğru sarkma yapar. Eskiler Bu engellemek için çalışanı makinanın arkasına sokup sacı yukarı doğru kaldırması istenirdi. İş güvenliği açısından son derece tehlikeli olan bu yöntemden vazgeçildi. Bunun yerine pinomatik sac destek sistemi olarak isimlendirilen sistem kullanılmaya başladı. Bu sistemde pinomatik olarak arka dayama kolları yukarı kalkarak bizim sacı istediğimiz gibi sürmemizi arka dayama ölçüsüne itilebilir. Kesim sırasında pinomatik katlanarak üst tablanın hareketini engellememiş olur. Kalın saclarda bu tarz bir sarkma olmayacağından kullanılmamaktadır.
Siyah ağırlıklı kesim yapan firmalar genel olarak NC kontrollü olanı tercih etmektedir. Paslanmaz malzeme kullanılan firmalar gerekli bilgilendirme yapılmadığından devirmeli giyotin makas yatırımı yaparlar, ancak çapaklanma daha fazla olduğundan istenen verimi elde edemezler. Paslanmaz kesimi yapan firmalar açı ayarlı giyotin makası tercih etmelidirler.
Lazer ve plazma makinaları geliştiğinden teknolojik olarak çok büyük farklılıklar olmamaktadır. Geçmiş dönemde kesim sonrasında sacı geri verme, otomatik konveyör , istifleme gibi sistemler kullanılmaktaydı.
Redüktörlü giyotin makas
Redüktörlü Giyotin makaslar genel olarak rulo açma hatlarında, seri kesim isteyen 4mm kalınlıklara kadar kullanılmaktadır. Bıçak boşluk ayarı giyotin makaslardaki gibi üstten değil alt tabladan ayarlanmaktadır. Redüktörlü makaslar dakikada 42 vuruş adedine çıkmaktadır. 3 metre 4mm (siyah) malzeme kalınlıklarına kadar kullanılmaktadır. Daha üstü için Redüktör sistemi uygun değildir. Kendi içerisinde farklı ebatlarda redüktörlü giyotin makaslar bulunmaktadır. Burada kullanılan Redüktör markası kızaklar kullanılan miller ve bıçak kalitesi ile fiyat farklılıkları ile karşılaşılmaktadır. Havalandırma, butik paslanmaz malzeme kesimi yapan firmalarda yaygın olarak görülmektedir.
Kollu giyotin makas
Bir dönemin vazgeçilmez bir makinası kollu giyotin makas şuan Türkiye’de sac işleme makinaları imalatı gerçekleştiren bir çok firmanın yola çıkış makinasıdır. Yapmak istediğimiz 1-1,2 mm saclardaki kesimlerde kullanılmaktadır. Seri iş yapmayan butik çalışan firmalarda kullanımı devam etmektedir.
Köşe Kesme Makinası
Köşe kesme makinaları genel olarak incelendiğinde, 2 tip olarak üretilmektedir. Sabit açılı ve açı ayarlı olarak kullanılmaktadır. Butik Paslanmaz mutfak işi yapan bir firma bir dolap imal etmek istediğinde, giyotin makas ile malzemenin ebatlarını ayarlar. Sonrasında Tava bükümü yapacak ise levhanın köşelerinden kesmesi gerekmektedir. Bu işlemi el köşe çıkarma olmadan eğer ince parça ise el makası ile kalın parça ise eksantrik kalıbında veya el plazması ile yapmak zorunda kalır. Köşe kesme makinası ile istediği ölçüdeki köşe boşluğunu oluşturmaktadır. Zaman içerisinde elektrik pano kapakları incelendiğinde faklı açılarda köşe kesme işlemleri yapılarak 3 farklı açıda kesim yapmak gerekiyordu. Açılı köse kesme makinalarında 30 dereceden 130 dereceye kadar farklı ölçülerde kesim yapmak mümkündür. Firma açıyı ayarladıktan sonra birinci kesimleri yapar bitirir. Sonrasından açı ayarını değiştirerek diğer kesimlerini gerçekleştirir. Köşe kesme, kollu makas gibi makinelerin lazer ve plazma tezgâhlarının artışı ile piyasadaki kullanım oranlarında azalma meydana geldi. Paslanmaz mutfakçı bir firmayı örnek alalım paslanmaz sacı aldı. Kollu veya redüktörlü bir giyotin makasta öcülerinde kesti. Yapacak olduğu büküme göre köşe açılarını ayarladı ve kesti. Bükme işlemini caka veya Apkant preste tamamladı. Sonrasında kenarlarına TIG kaynak işlemini yapıp köşe parlatmalarını gerçekleştirip paslanmaz dolap kapağını üretmiş oldu.
Daire Kesme Makasları
Daire kesme Makinası butik işlerde, havalandırma, soba gibi sektörlerde lazer veya plazma tezgâhlarının kullanılmadığı zamanlarda bir levha üzerinden belirli minimum ve maksimum çap özelliği olan makinalarda kullanılan bir makinadır. Ayarlanan çapa kesim için malzeme makine üzerine bağlanır. İki disk şeklindeki bir bıçağın arasında kesim işlemi gerçekleştirilir.
Punch Pres
Malzeme şekillendirmede önemli bir üretim makinasıdır. Bir sac levha üzerinde çeşitli kare, yuvarlak gibi bir boşatmaları yapmak için üretilen bir makinadır. Kullanım ebadına göre 1000×1250, 1250×1500 ve 1500×3000 gibi ebatlarda Panç presler bulunmaktadır. Geçmiş dönemlerde kafa üzerinde 6 adet kalıp veya büyük tek kalıp bağlanabilen pançlar vardı. Burada belirli bir çaptaki delikleri yapacak olan alt ve üst kalıp ayarlanır, kaç adet varsa bu işlemleri tamamlar, sonrasında diğer kalıp için makine durur, yeni kalıp ayarlanıp kesime devam edilirdi. Kesim üzerinde açılı bir kesim varsa kalıp yönünü değiştirmek gerekiyordu. Burada CNC bir kontrol sistemi kullanılmaktaydı. Gelişen teknoloji ile makine üzerindeki kalıplar Multitool olarak isimlendirilen kalıp sistemli makinalar üretildi. Bağlama çapına göre üzerinde bulunan kalıpları alt ve üst kalıp olarak otomatik döndürüp hidrolik pistonun altına getirerek sert bir basınç ile malzemede boşaltma işlemini gerçekleştirirdi. Gelişen teknoloji ile Taret panç denilen üzerine çok faklı kalıpların bağlandığı modeller üretildi. Böylelikle Takım değiştirme gibi zaman kaybetmeden tek seferde bitmiş ürün alınmaya başlandı. Günümüzde hidrolik olarak dakikada 600-900-1200 vuruş yapan makinalar bulunmaktadır. Hidrolik sistemden basınç işlemini servo motor ile gerçekleştirilen makinalar da kullanılmaktadır. Punç sadece delik, ebatlama, kare gibi parçaları kesmenin yanında değişik formlardaki kabartmaları gerçekleştiren ürünlerde üretilmektedir. Kalıplarda yaşanan aşınmalarda taşlama işlemi yapılarak kalıplar kullanılmaya devam etmektedir. Taşlama ile kurtarmayan takımlarda sadece uç kısımları değiştirilerek kullanılmaya devam eder. Taret üzerinde bulunan tutucular değiştirilmez. Taret panç makinaları genel olarak takımsız satılır. Sizin yapacak olduğunuz işe göre sonradan takımlandırılır. Bu yatırım yeri gelir makine fiyatına bile yakınlaşır. Taret panç preslerde alt ve üst uyum makinanın kalitesini göstermektedir. Alt ve üzer kalıbın merkezlenmesinde yaşanacak sıkıntılar çapaklarai takımların aşınmasına sebebiyet vermektedir. 6mm kadar kullanılan panç presler bulunmaktadır. Ancak kullanım olarak 2mm üzerine pek çıkılmaz. Kalın kesimlerde takım aşınması daha fazladır.
Lazer Kesim
Metal levha kesmek için, çeşitli CNC makine tezgahları bulunur. En önemli teknikler plazma, su jeti ve lazerdir. Her farklı teknik, uygulamaya bağlı olarak kendine özgü avantajları da beraberinde getirir. Ancak şekilli hatların ve hassas şekillerin kesimi söz konusu olduğunda en iyi çözümü lazerli kesim sunar. Aynı zamanda frezelemeye de iyi bir alternatif sağlar.
Günümüzde sağlıktan, teknolojiye, askeri alandan eğlence hayatına kadar bir çok alanda kullanılıyor lazer. İlk çalışan optik lazer 1960 yılında Theodore Maiman tarafından yapıldı, ancak lazer’in bulunuş öyküsü 1900 lü yılların başında Albert Einstein ile başlamıştır.
Albert Einstein‘ın Teorisi
Lazer İngilizce de Laser (Light Amplification by Stimulated Emission of Radiation) için kullanılan bir kısaltmadır. Temelde Lazer atom veya molekül enerji düzeyleri arasındaki elektron geçişleri ile oluşan ışık fotonlarına dayanır. Uyarılmış emisyon yoluyla ışık üreten bir cihazdır. Albert Einstein 1917 yılında, geri uyarılmış emisyon teorisini öne sürmüştür.
Laser Kavramı
1958 yılında, Charles Townes ve Arthur Schawlow maser (short for microwave amplification by stimulated emission of radiation) i geliştirdi. Laser, lazerin gelişiminde çok önemli bir yer tutmaktadır. Laser uzay araştırmalarında radyo sinyallerini güçlendirmek için kullanılmıştır.
İlk Lazer
Laser’in bulunuşundan iki yıl sonra 1960 yılında Theodore Maiman ilk lazeri oluşturdu. Ancak Gordon Gould lazer kelimesini 1957 yılında kullanan ilk kişi oldu.
1957 yılında optik lazer için Gordon Gould tarafından yapılmış icat vardı fakat patent alabilmek için çok da başarılı bir proje değildi.
Gordon Gould kendi icat ettiği lazer için patenti 1977 yılında alabildi. Bu nedenle Theodore Maiman ‘nın yaptığı lazer gösterisi ilk başarılı lazer olarak kabul edilmektedir.
1960 yılında Javan gaz lazeri icat etti. Bu elektrik enerjisi değişimini lazer içinde ilk kullanılışı olarak tarihe geçti. Bunu 1962 yılında yarı iletken lazer’in Robert Hall tarafından bulunuşu izledi. İki yıl sonra Kumar Patel, karbondioksit lazeri ve Hal Walker telemetri lazer buluşları geldi.
Fiber lazer ve CO2 arasındaki en temek fark üretilen lazer ışınının dalga boyudur.
Fiber lazerler için lazer ışınının dalga boyu ~1µm iken CO2 lazerin dalga boyu ~10µm dir.
Türkiye’deki lazer kesim tezgahları üretimi 2010 yıllarına doğru başladı. Daha önce yurt dışından gelen lazer tezgahların fiyatları çok yukarılardaydı. Yerli üretimin artması ile yurt dışından gelen makinaların fiyatları neredeyse yarı fiyatına indi. Yerli üretim makinalar gelişmesi ülke ekonomisine çok katkıda sağladı.
Yukarıda da belirtildiği ilk olarak CO2 lazerler aktif olarak kullanılıyordu. Sonrasında Fiber lazer olarak adlandırılan katı hal lazerleri çıktı. Burada Co2 lazerdeki gibi ışın oluşturmak için herhangi bir gaza ihtiyaç duyulmadı. İlk başlangıç serüveninde 2 kw değerlerinde fiber lazerler üretildi. Kullanım maliyetleri Co2 ile karşılaştırıldığından muazzam ekonomik olduğu görüldü. Karşılaştırma kriterlerinde KW değerleri eşit olmadığı için kalın malzemelerde Co2 lazer avantajını koruyordu. Sonrasında 4 kw lazerler çıktı, kalın parçalarda biraz rakabetçi olunmaya başlandı. Sonrasında 6kw 8kw 10 kw 12 kw ve 15 kw lazer güç üreteçleri geliştirildi. Ülkemizde yaygın olarak 4 kw fiber Lazer makinaları bulunmaktadır. 6 kw yeni yeni yaygınlaşırken yaşanan gelişmeler ile 8 kw yaygınlaşmadan 10 kw lazer üretimine başlandı. Lazer üreticilerinden DENER makine markası 12 kw lazerini 2019 yılı sonunda çıkaracağını belirtiyor. Bu gelişmeler ile Co2 lazer sıfır yatırımı yapan neredeyse kalmadı denilebilir.
Fiber lazerlerde Diyot ömrü olarak 100.000 saat çalışmadan bahsedilmektedir. Ancak Kullanım sırasındaki parametreler, soğutma, yansıtma gibi olumsuzluklardan modüllerde arızalar meydana gelmeye başladı. Burada da fiyat anlamında firmalara 10.000 -40.000 € arasında arızalar meydana gelmeye başladı. Son kullanıcı olan müşterinin bu konularda çok tecrübeli bir operatör kullanması gerektiği anlaşılmaktadır.
Yerli fiber lazer makinalarını inceleyecek olursak;
Belirli bir kapasite üstünde olan sac işleme makinaları üreten firmalar incelediğinde lazer güç üreteci Kw değerleri aynı olduğunda genel olarak kesim kalınlıkları ve kesim hızları aynı değerlere yakındır.